Fadir means Father from the Old Norse — a name embodying our desire for our tools to be passed down from generation to generation, from father to son. We want your grandchildren to remember their childhood spent working in their dad and grandpa's garage many years from now. In our forge, each axe is thoroughly handcrafted, eschewing piecework arrangements to allow our smiths the time and dedication needed to create superior axes. Our axes undergo minimal post-production work, ensuring the integrity of the forging process remains evident.
Forging and Forming the Axe Head
We have sourced our steel from a small metallurgical enterprise in the Lugansk region for many years. Different kinds of steel from there were used to construct bridges, airports, and stadiums across the country. But when the full-scale war erupted, getting materials from the region became impossible.
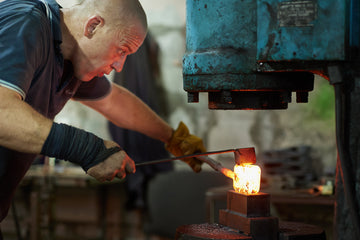
We faced a challenge: finding a new supplier to match the quality we relied on. In our search, we discovered a remarkable company in Dnipro. This enterprise, run by a family whose roots in metallurgy go back to 1948, became our new partner. The hereditary owner, a true master of his craft, ensured that their steel met the highest standards. The quality, tested by time and certified by rigorous standards, was exactly what we needed to maintain the durability and reliability of our tools. This partnership allowed us to continue producing the superior tools our customers expect, ensuring that each piece could withstand the test of time and be passed down through generations.
So, crafted from a special alloy of recycled steel with a high carbon content, each Fadir's axe begins its journey in the fiery heart of our forge. The steel is heated to a blistering 900°C before our skilled blacksmiths deftly manipulate it under the force of a powerful press, delivering 80 strikes per minute with a staggering 80 kg of pressure in each blow. This process allows the steel to gradually transform from raw material into the finely honed edge of a finished axe head, which is durable and precise.

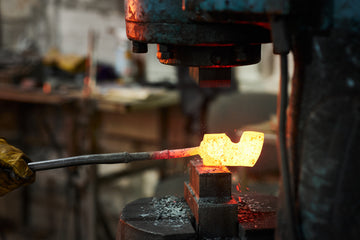
Grinding, Hardening, and Tempering
We make axes the same way they were made hundreds of years ago, and accordingly our next steps are grinding, hardening, and tempering. The initial coarse grinding shapes the edge, preparing it for the critical hardening process. We heat the edge to a blistering 850°C, then plunge it swiftly into the water, a dramatic process that locks in exceptional hardness.
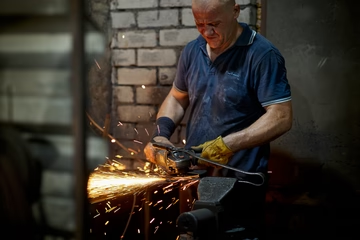
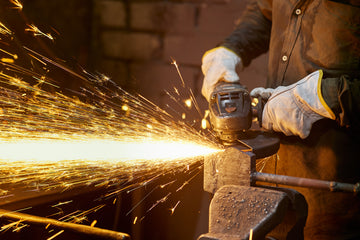
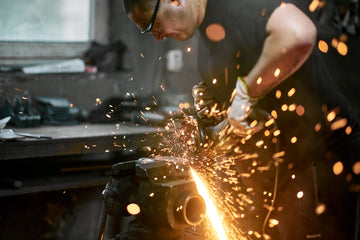
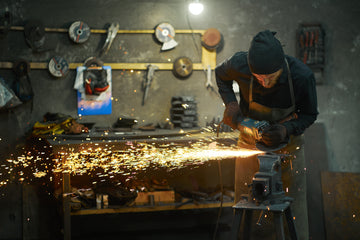
Yet, this intense procedure introduces stresses within the steel, where the tempering process comes into play.To achieve the perfect balance of hardness and flexibility, we temper the steel in an oven at 180°C for an hour. This careful tempering relieves the internal stresses, ensuring that the axe is not only incredibly hard but also resilient and durable. Each step from grinding to tempering is done with care and precision that transforms raw steel into a trusted tool meant to last for generations.
Tumbling and Sharpening
After the initial grinding, tempering, and annealing, each axe head undergoes a meticulous tumbling process with small ceramic balls. This step removes any residual scale from the forging and enhances rust resistance, giving the axe a clean, polished finish.We then put the axe through rigorous hardness and integrity tests to ensure it meets our exacting standards.
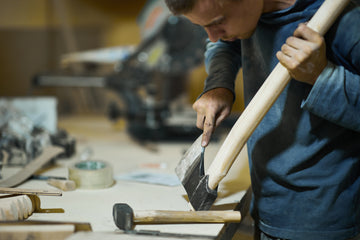
Only after passing these assessments do we sharpen and polish the edge to a razor-sharp finish. This painstaking process, rooted in tradition, ensures that every axe we create is more than just a tool — it's a legacy.Our founder's favorite childhood film is Commando. One scene in particular, where Schwarzenegger's character sees his daughter's reflection in an axe blade, left a lasting impression. Inspired by that episode, we do our polishing perfectly.
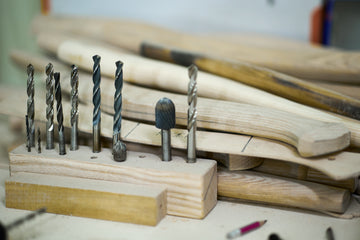
Fitting the Axe with a Handle
The axe head is dipped in a water-resistant anti-rust oil before carefully fitted with an ash tree handle. It is manually fixed into the axe head and reinforced with a wooden wedge, ensuring stability and longevity.The wood for our axes is ash, chosen for its strength, water resistance, and durability. It aligns perfectly with our philosophy of quality—we want our axes to be passed down from father to son, from generation to generation.The ash trees we use are not just any trees.
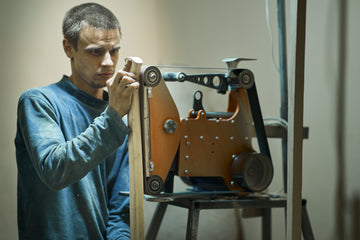
They are brought from the rich lands of Polissia and the Ukrainian Carpathians to our workshop in the extreme northeast of the country. This journey, this connection to the land, is what makes our axes special. Each piece of wood has its own unique story, a story that is deeply rooted in our heritage. For instance, trembitas, our shepherds' centuries-old instruments, are also made from Ukrainian ash. When freshly cut ash arrives at our workshop, the air fills with the scent of a spring forest after rain. On days like these, we especially love our work.
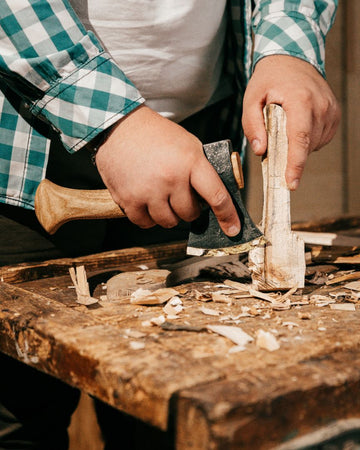
Quality Control and Assurance
When we started making axes, it didn't go smoothly at all. We had to discard many defective tools and often found ourselves stuck, wondering if this idea would ever work out. It was surprising — and a bit flattering — that people still bought those early, flawed axes. Yes, we've come a long way with meticulous calculations, detailed drawings, and a solid quality control system. I'm genuinely proud of the tools we produce today.
Our commitment to high quality is more crucial than ever, as our axes are now used by the Ukrainian military. They're essential for building fortifications, improving life in tough terrains, and even preparing meals. It's a matter of pride for us that our tools stand as unbreakable as our defenders, supporting them in their noble mission.
Each approved axe comes with a protective leather sheath, ensuring it's ready for anything.